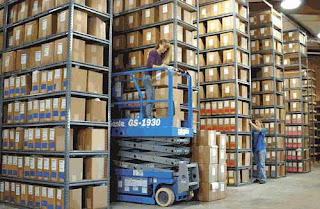
Standard costing is an important subtopic of manufacturing cost accounting. Standard costs are associated with manufacturing companies and are utilized to manage the costs of direct material, direct labor, and manufacturing overhead.
In lieu of assigning actual or average costs of direct material, direct labor, and manufacturing overhead and rolling these costs into their products, most manufacturers assign a standard cost to their systems. This means that their inventories and cost of goods sold are valued using the standard costs, and not the actual or average costs, of a product. The Manufacturers pays their vendors at actual costs which can vary over time. This results in differences between the actual costs and the standard costs, and those differences are known as variances.
Standard costing and the related variances are valuable to measure the performance of inventory and product production. When a variance arises, management becomes aware that manufacturing costs have differed from the standard (planned, expected) costs.
- If the actual cost is greater than the standard cost the variance is referred to as unfavorable; and unfavorable variances result in the company’s actual profit being less than planned.
- If the actual cost is less than the standard cost the variance is referred to as favorable; and favorable variances result in the company’s actual profit being less planned.
Timely reporting of these manufacturing variances allows management to take action on the differences from the planned amounts.
This, however, is not the only reason that manufacturers utilize standard costs. In the manufacturing process, materials are issued to work orders and job orders and taken out of the perpetual inventory and show up on the balance sheet on what is known as work in process. Because work in process no longer has any part number identity, it is retained as a gross value on the balance sheet. If a part is issued to a work order and the value of that part is written to the general ledger work in process account at its current value. If the company were using average cost to value their products and the item in question is received at a higher price prior to the work order being completed, then the item will be relieved from inventory in the future at the new value, causing a negative balance in the work in process account. Multiply this by thousands of transactions and you will see why it is important to utilize standard costs in a manufacturing system.
The perpetual inventory is maintained at standard cost (including Direct Materials and Subassemblies), and the standard cost of finished goods becomes the sum of the standard costs of the following values:
- Direct material
- Direct labor
- Manufacturing overhead
- Variable manufacturing overhead
- Fixed manufacturing overhead
Thanks alot for the info ....i would like to know more about how to calculate standard cost when the order containes configured items and includes routing cost ....
ReplyDeleteTypo in the 2nd bullet. If the variance between actual cost and standard cost is favorable the profits are more than expected, not less. In the two cases in the bullet points, both are "less" profits for the company.
ReplyDelete